If the tail falls off an aircraft in flight, it’s usually bad. It would not make for a very happy new year. It happened in the USA, to a Sting like ours. The whole horizontal stabiliser fell off and the aircraft ended up in a Florida field looking like this:
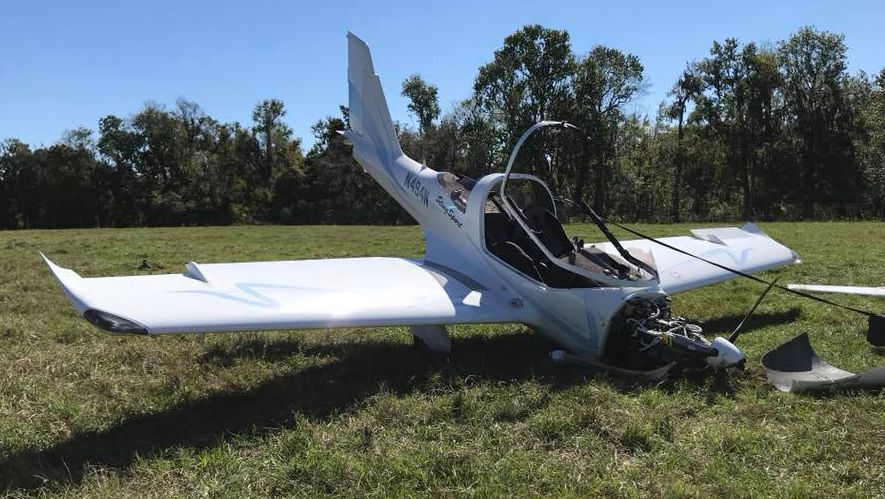
Pretty much wrecked, but the single occupant walked away. It probably would have been fatal if not for the built in parachute rescue system…
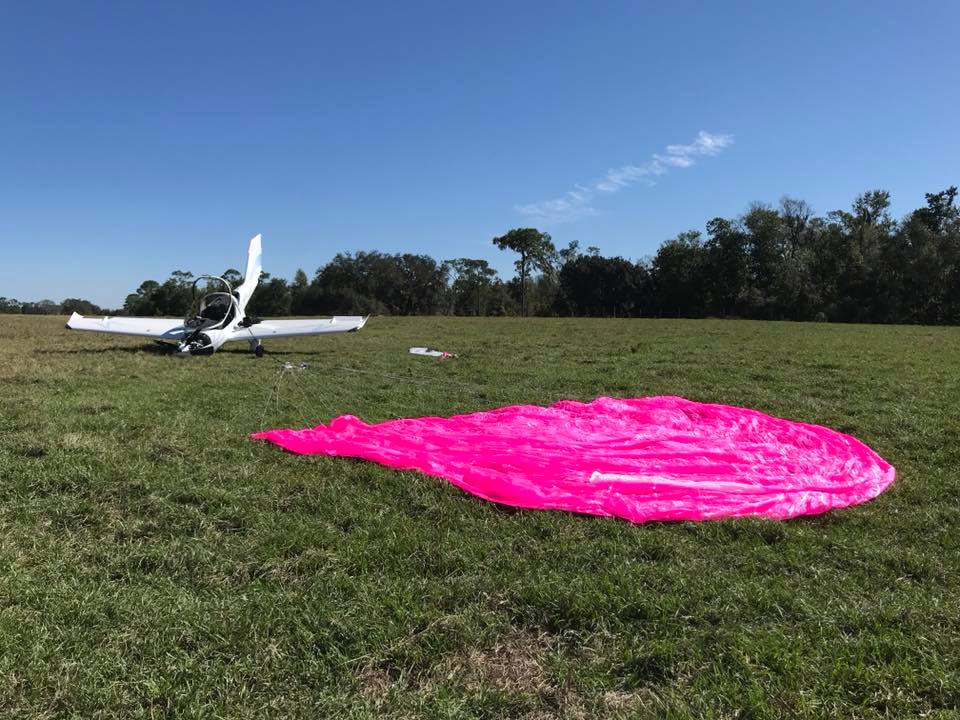
( Both crash photos courtesy of http://www.kathrynsreport.com/2018/11/tl-ultralight-sting-sport-n494n.html )
Because of this we had an Airworthiness Information Leaflet mandating an inspection of the horizontal stabiliser mounting pins within 5 flying hours and thereafter every year. Hearsay is that the mounting pins of the Florida crash aircraft were severely corroded.
Senior Engineer Brenda helped to remove the stab once the controls had been disconnected. Here she is peeling off silicone, the maintenance manual says the stab should be reattached in a bed of the stuff. It reduces vibration and helps keep the stab in place, but can be a real pain to remove once the tailplane is off the aircraft:
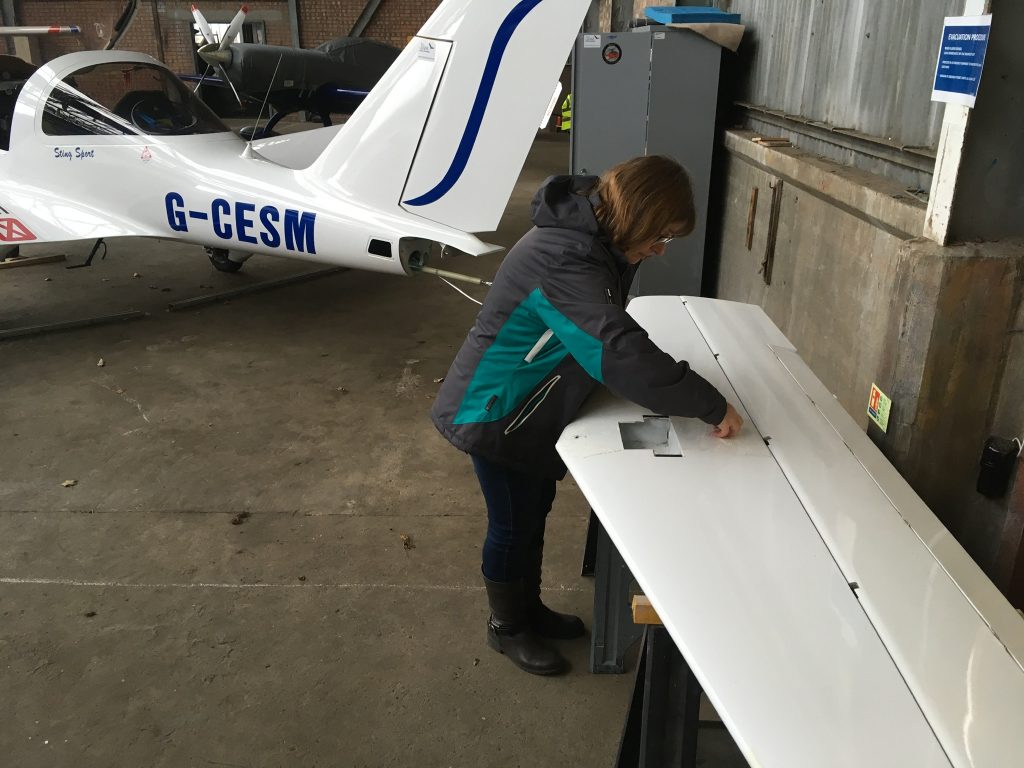
We also found a good use for our Nando’s card, it was great for gently scraping off the old silicone:
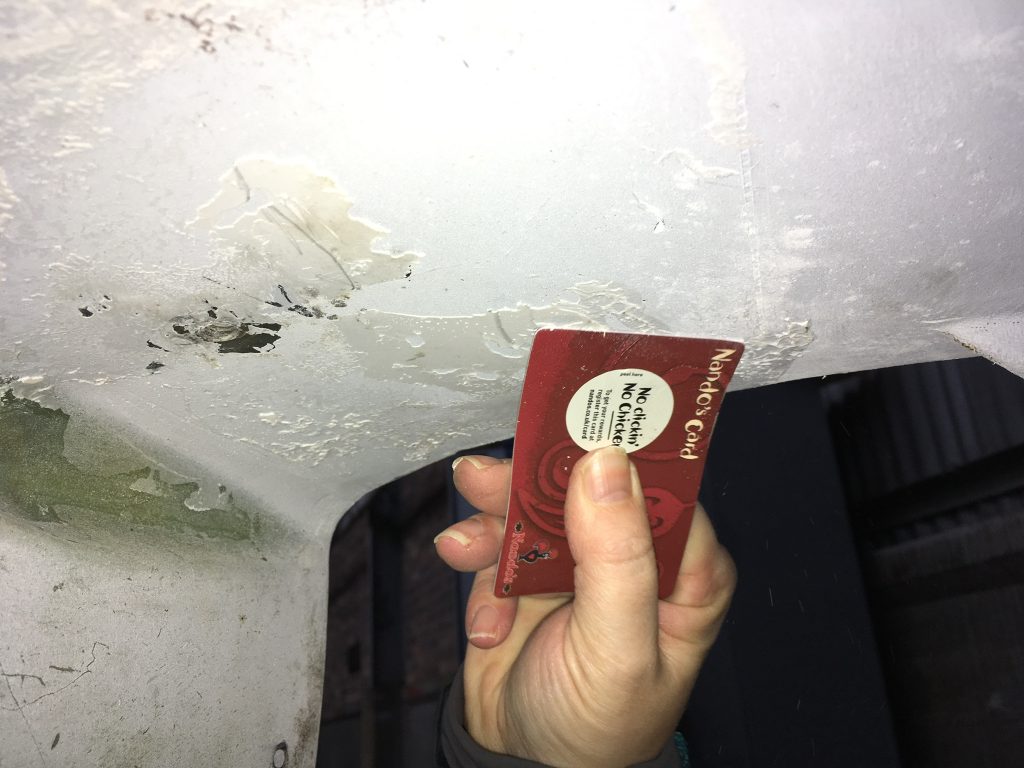
Our pins didn’t look corroded at all, nice and shiny. They passed the inspection and just needed a little polish and regreasing before reassembly:
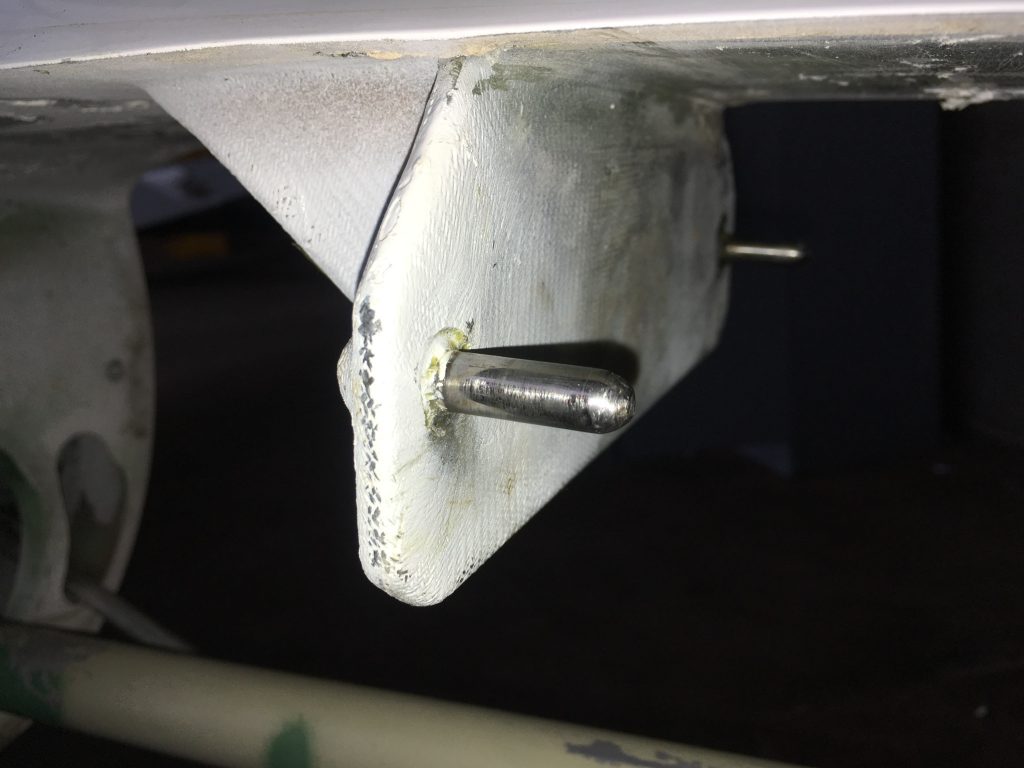
Once inspected, the world’s coolest copilot helped with the reassembly (Thank you, Rory), and then I did battle with reconnecting the controls. Lots of fiddly washers in the elevator and trim control connections:
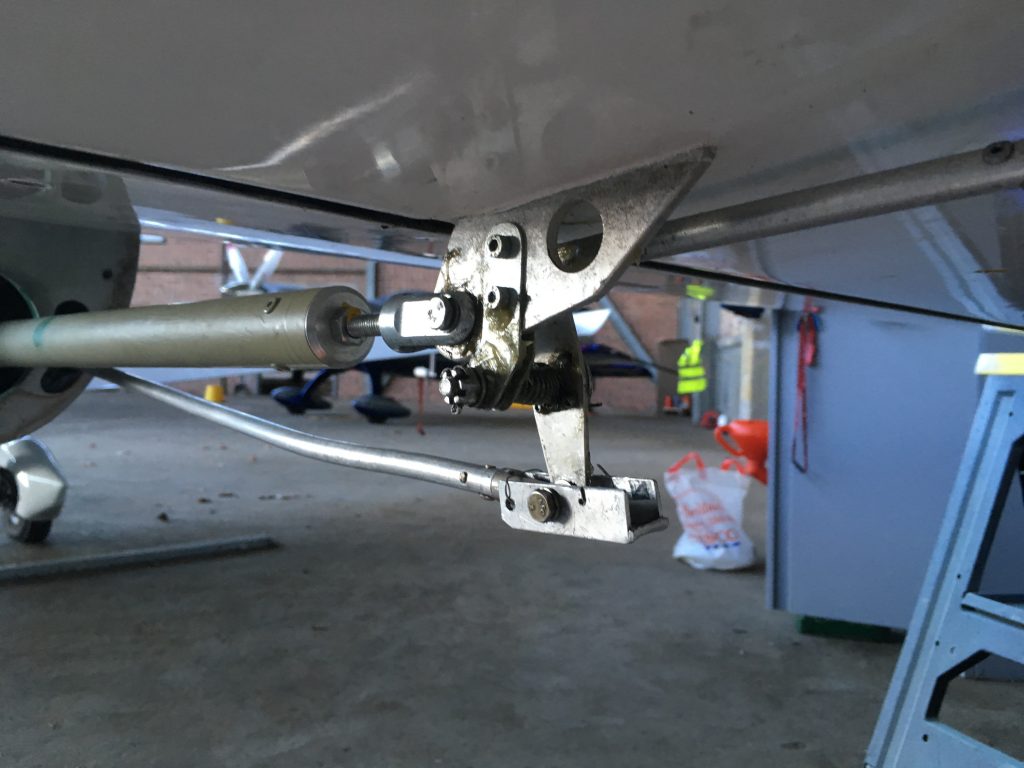
The connectors were reassembled “dry” with no grease, for ease of inspection, and then lubricated once inspected. Every critical system needs a duplicate inspection if it is disturbed; I do one as part of the reassembly process and Sandy my inspector does another, we both sign in the aircraft logbook.
Another reason for reassembling “dry” is that washers are very slippery and can ping off into the distance if given half a chance. Check the dark corners of any hangar and you’re bound to find one. Here’s the greased up final product:
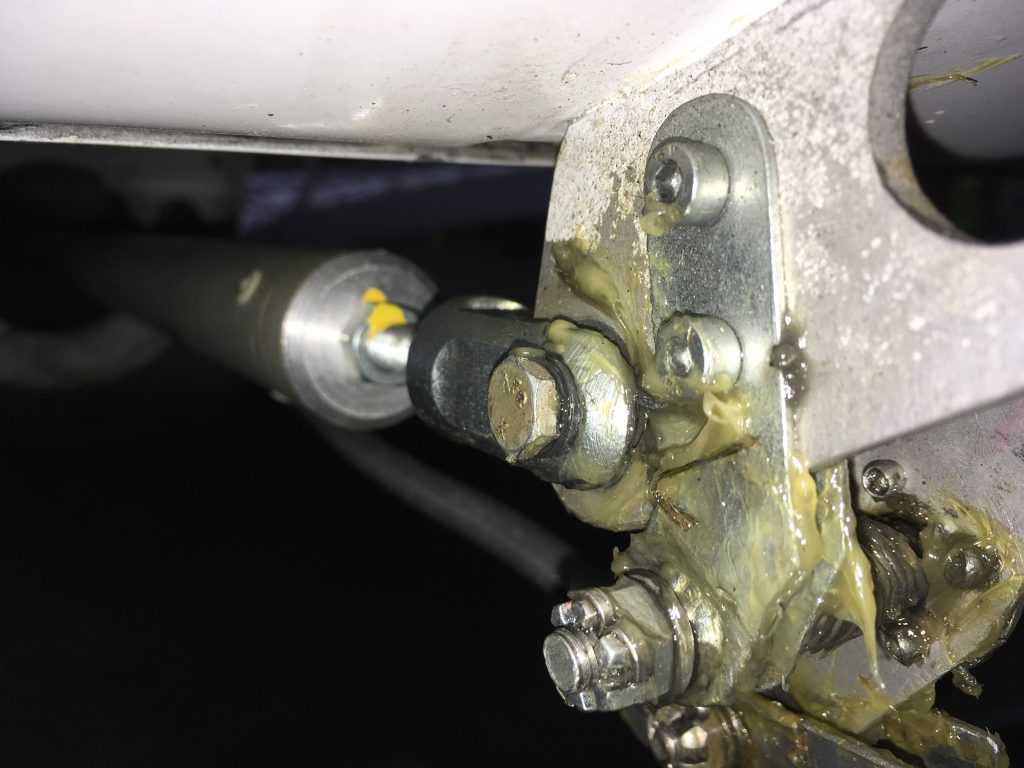
Finally came the wire locking of the mounting bolt and reattachment of the fairing. I was having a hell of a time holding the torch while wire locking and eventually ended up taping it to the elevator control rod. If only I had thought of that earlier…
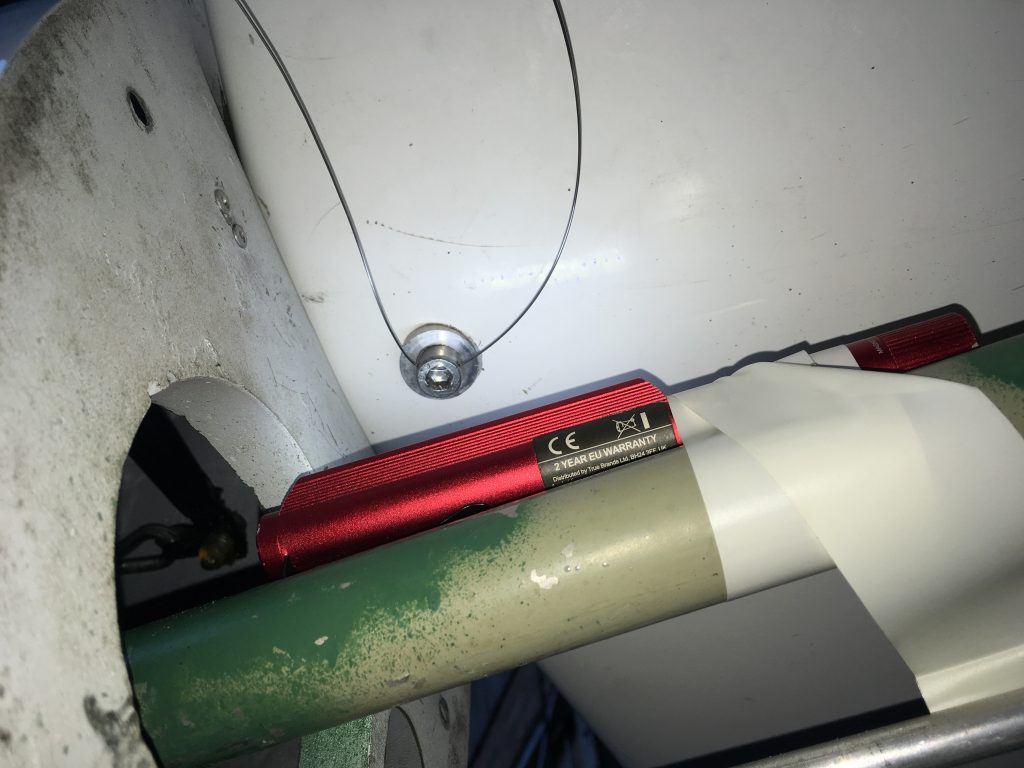
Aircraft inspected and reassembled, paperwork all in order and logbook signed up, it was time to go flying…
…and the engine wouldn’t start. The battery had been sitting in a (very) cold hangar for over a month and just wasn’t up to the job.
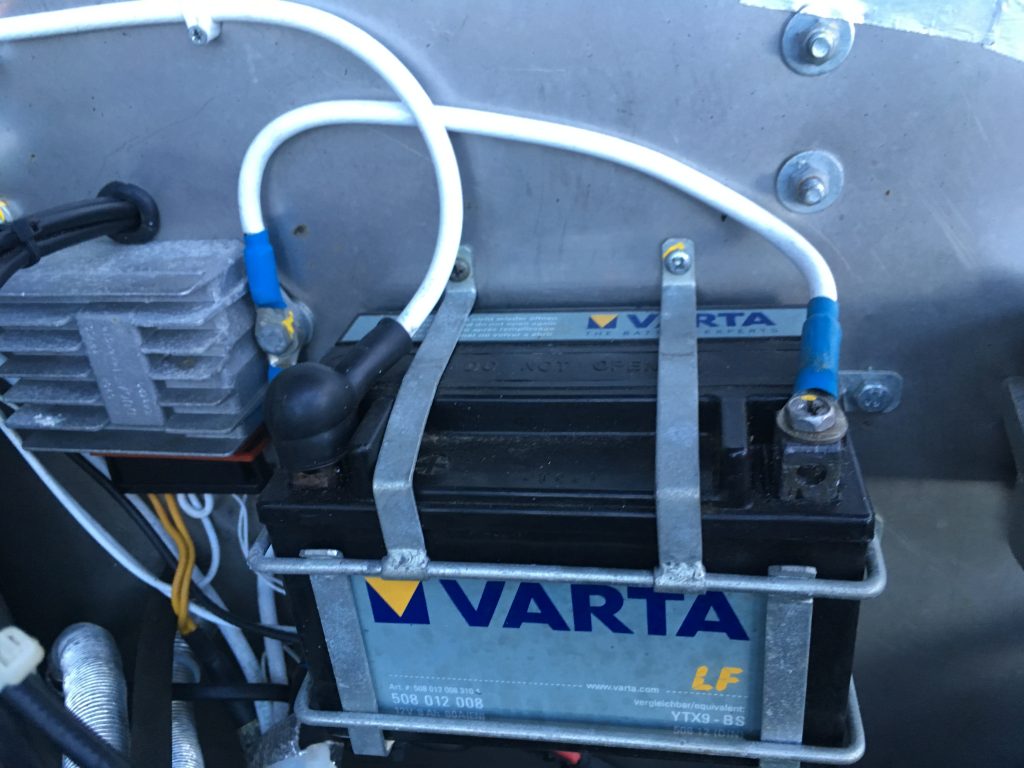
There are some awesome videos at “Sting Flight” on YouTube, see https://www.youtube.com/channel/UC0avm_9h4lpS5sIcQaBCQ_A – producer Rich DeHaven says that a battery lasts about 200 hours – ours has made it to 300 or so. It has done well but it’s about time for a change.
Luckily the battery in the Sting is a popular model, also used in quad bikes and snowmobiles, so it doesn’t have the big aviation markup normally associated with aircraft parts. A pleasant surprise to not pay through the nose for bits for the aircraft.
Just waiting for the new battery to arrive…the weather is lovely, and we’re stuck on the ground. Grrrrr.