Cowlings back on again, for the first time in months:
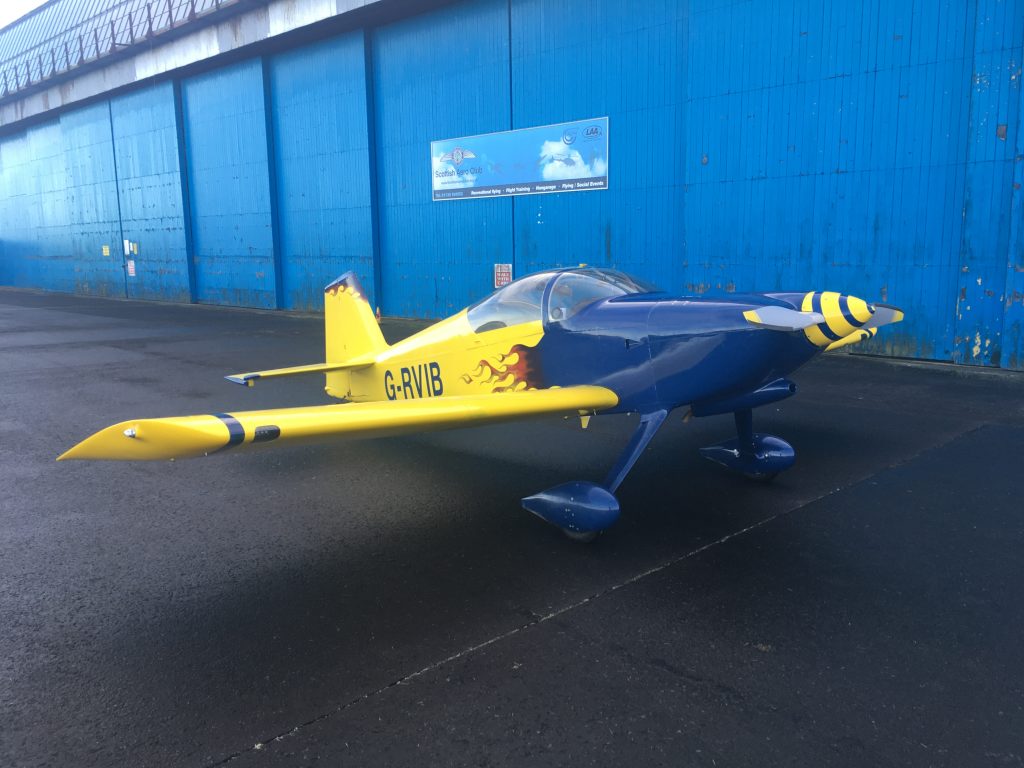
Since the end of July, we had a bit of tinkering to attend to:
Sump oil leak, cylinder head cover oil leak, carburettor sent off for refurbishment, dead number 1 cylinder (new piston rings and cleaned up valves), dead battery and dodgy starter motor.
Finally everything was back together and ground runs completed. No excuse to put it off any longer. Time to fly.

A general wazz around just to the north of the airfield, keeping close in case we needed to get back in a hurry. Note the trace showing a simulated circuit pattern just over the A984 symbol…this was to check the engine response in a balked landing when full power is needed in a hurry.
All was satisfactory so it was back to the airfield for circuit practise. This was to exercise the engine through the whole range of power settings and had the added benefit of landing practise for me.
With hardly any wind the duty runway was the east west one. This goes right past the clubhouse windows. And everybody is watching (and grading) the landings. No pressure, then…especially as fellow helicopter pilot Chris (who also flies an RV3 and is building an RV14, see http://www.vansrv14.uk/) had just landed and was undoubtedly watching with the rest of the vultures.
Several landings later and the aircraft was still in one piece and capable of being taxied off the runway, so the landings can’t have been TOO bad. The RV grin is back!

As usual the landing debrief from the gallery was brutal. They take no prisoners. Not to worry, the aircraft flies again! Plus it was time for me to join the grading team and watch some landings for a bit…no pressure!